当社では、人の目、人の手を活かしたものづくりを大切にしています。
担当者が想いを込めて一つ一つの製品を丁寧に作ることで、
安心安全、高品質な製品づくりを目指しています。
当社では、人の目、人の手を活かしたものづくりを大切にしています。
担当者が想いを込めて一つ一つの製品を丁寧に作ることで、安心安全、高品質な製品づくりを目指しています。
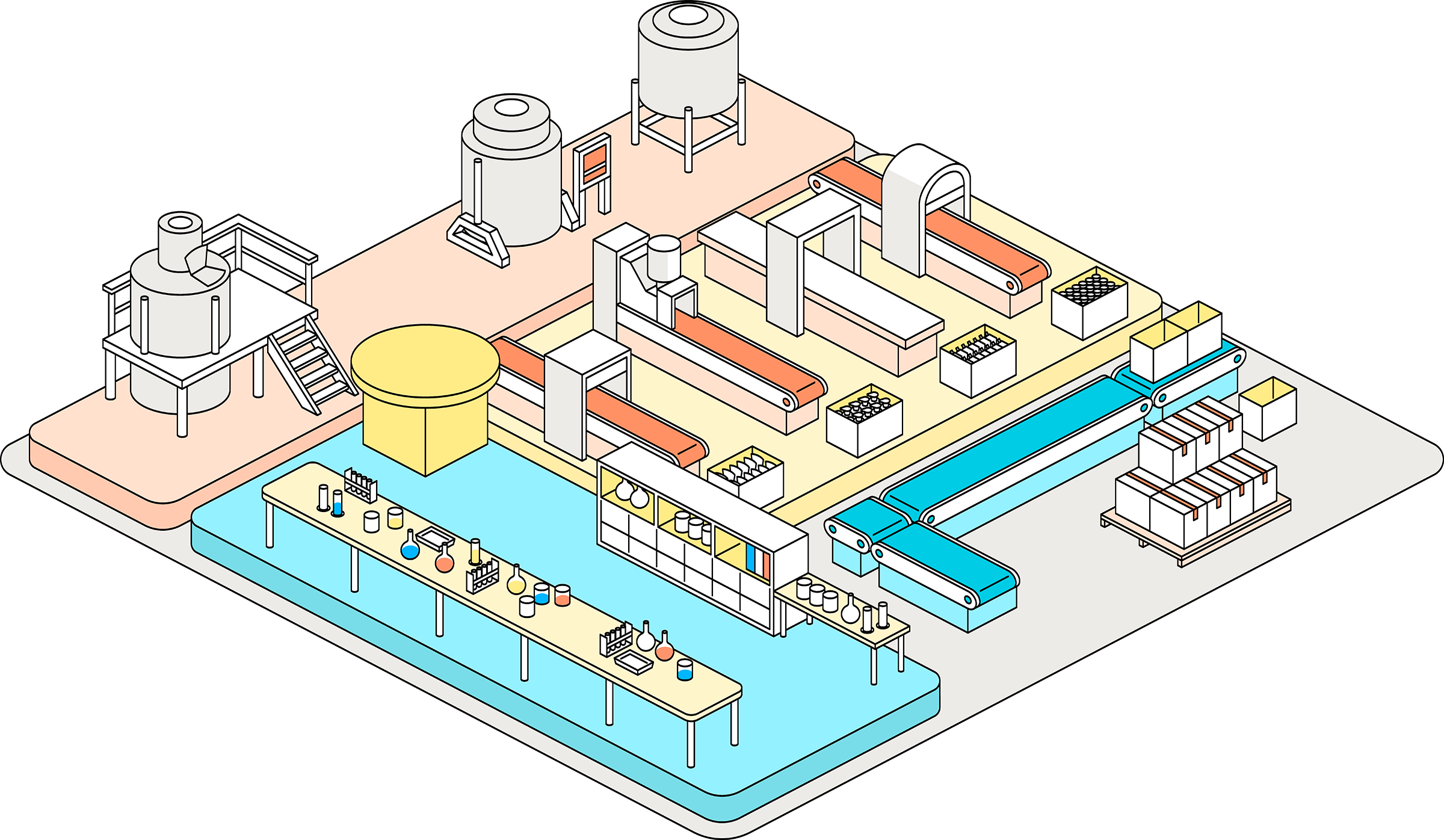
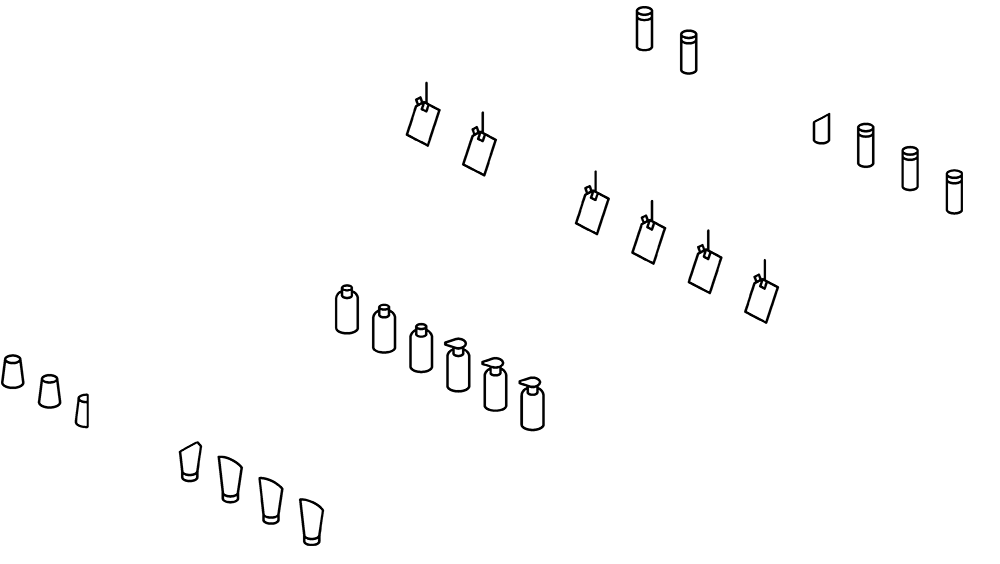
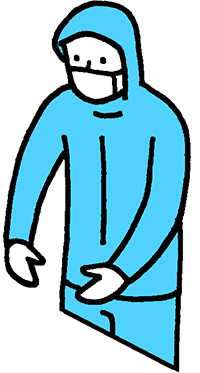
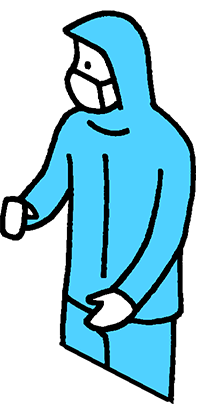
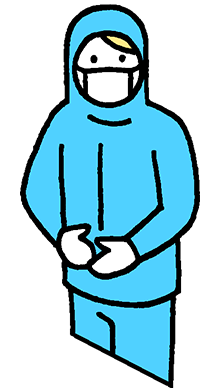
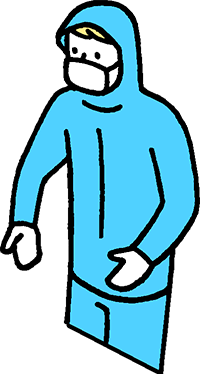
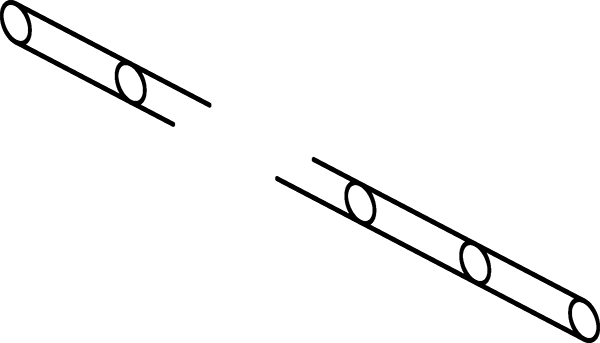
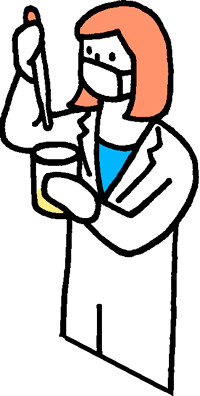
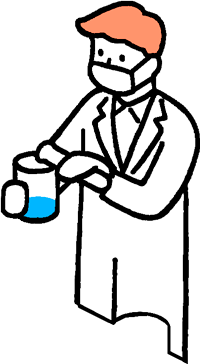
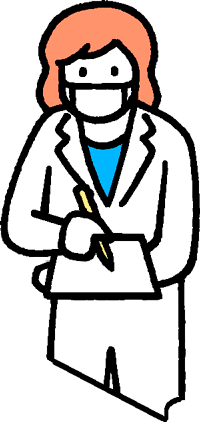
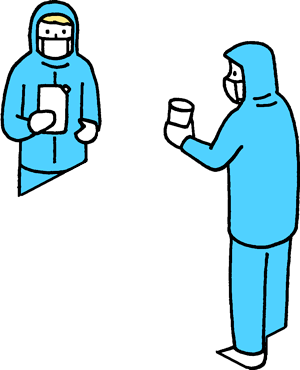
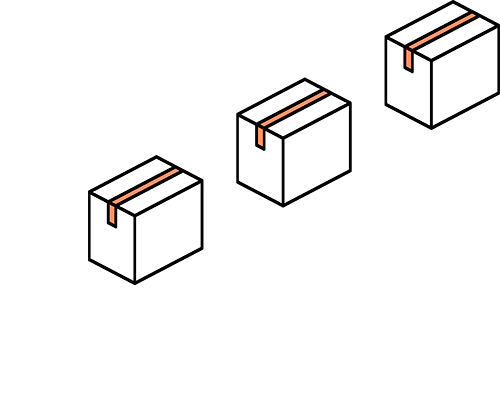
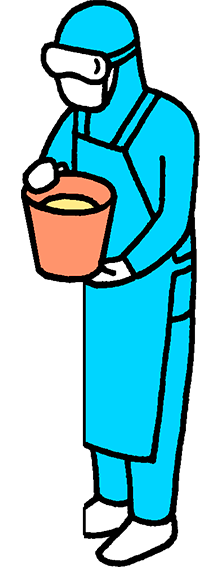
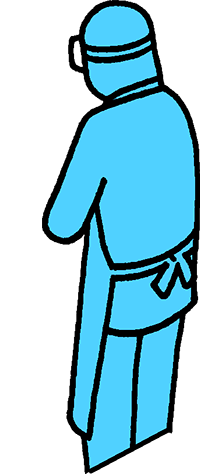
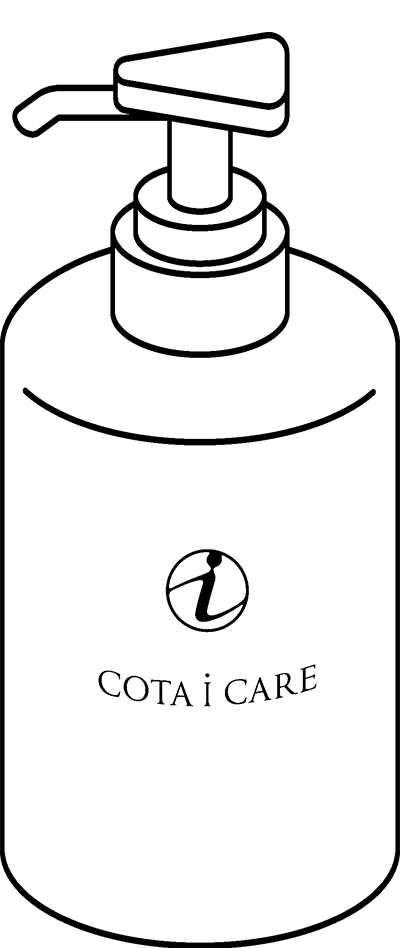
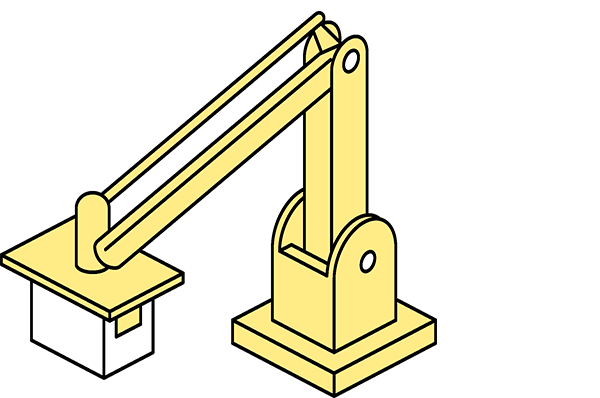
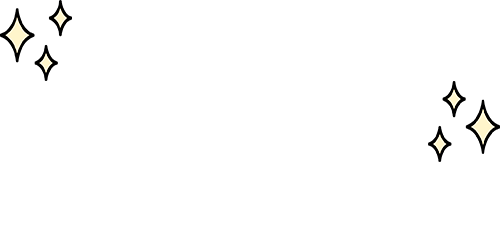
※イラストはイメージであり、実際の工場とは異なります。
Development & Production
コタのものづくり
変わるよろこびを、すべての髪から。
自然のやさしさと科学の力を融合させながら、徹底したお客様目線で、ニーズに適った製品開発を日夜追求しています。
品質はもちろん、人にも環境にも安心・安全であることを基本に原料にもこだわり、
厳しい品質チェックと改良を幾重にも重ねる地道なプロセスを経て、お客様の髪を芯から美しくする製品が誕生します。
そして、オートメーション化が進んだ生産現場において、今なおきちんと「人の目」と「人の手」を活かしたものづくりを続けながら、ゆるぎない想いが詰まった安心・安全、高品質な製品を作り上げています。
ものづくりのこだわり(安心・安全編)
ネイチャー&サイエンス
コタ独自のナノ化DDS技術を用いたナノ化育毛成分ユニットの開発について
コタオリジナル ナノ化育毛成分ユニットの実力と効果